Изготовление пресс форм
Высокая точность – Современные пресс-формы изготавливаются с допусками до 0,01 мм, что обеспечивает стабильное качество литья.
Сложная конструкция – Состоят из матрицы, пуансона, системы литников, охлаждения и выталкивания, требующих точной подгонки.
Долговечность – Срок службы зависит от материала: - Алюминиевые – 5–50 тыс. циклов, - Стальные (P20, H13) – 100–500 тыс. циклов, - Твёрдые сплавы – 1 млн+ циклов.
Специализированные материалы – Используются инструментальные стали (P20, H13, NAK80), алюминий, медь-бериллиевые сплавы и покрытия (TiN, DLC).
Горячеканальные vs. холодноканальные системы – - Горячеканальные – дороже, но экономят материал и ускоряют цикл. - Холодноканальные – дешевле, но требуют обрезки литников.
3D-печать и аддитивные технологии – Позволяют создавать конформные каналы охлаждения и ускорять прототипирование.
Автоматизация – Современные пресс-формы интегрируются с роботами-загрузчиками для массового производства.
Микрообработка – Позволяет создавать текстуры и микрорельефы (например, "под кожу" или матовые поверхности).
Термообработка и покрытия – Закалка, азотирование, хромирование увеличивают износостойкость.
Экономическая эффективность – Окупаемость пресс-формы зависит от тиража: - Малые серии – выгоднее алюминиевые или 3D-печатные формы. - Массовое производство – требуются высокопрочные стальные пресс-формы.
ЧТО МЫ ПРОИЗВОДИМ
Пресс-формы для небольших тиражей
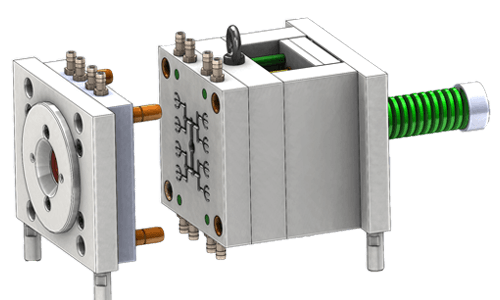
- Одно- или многоместные (одногнёздные / многогнёздные)
- Одногнёздные – производят одно изделие за цикл (подходят для крупных деталей или малых серий).
- Многогнёздные – несколько одинаковых изделий за один цикл (увеличивает производительность).
- От 2 до 8 мест.
- для литья ПНД, ПП, АБС - пластиков.
- Срок изготовления 8-12 недель.
- Гарантийный ресурс до 1000 тыс. циклов.
- Стоимость от 800 до 1500 т.р.
Двухплитные и трёхплитные пресс-формы
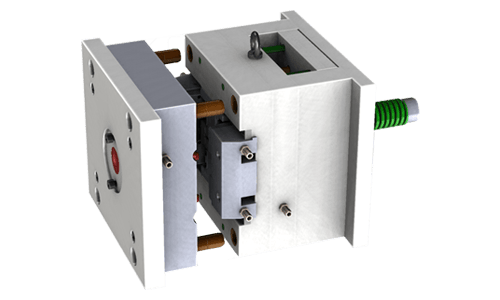
- Двухплитные – базовая конструкция (подвижная и неподвижная части), подходит для простых деталей.
- Трёхплитные – имеют дополнительную плиту для автоматического отделения литниковой системы, применяются для сложных изделий.
- Срок изготовления 8-12 недель.
- Гарантийный ресурс до 1000 тыс. циклов.
- Стоимость от 600 до 1500 т.р.
Пресс-формы с холодноканальной и горячеканальной литниковой системой
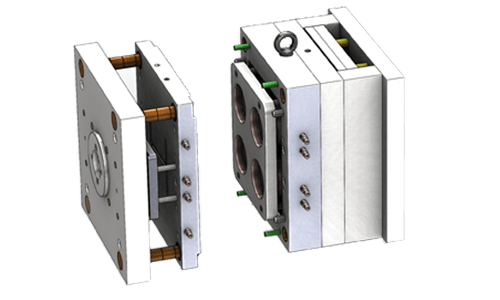
- Холодноканальные – литник затвердевает и удаляется вместе с изделием (дешевле, но больше отходов).
- Горячеканальные – литниковая система подогревается, материал остаётся расплавленным (меньше отходов, выше скорость литья).
- Срок изготовления 8-12 недель.
- Гарантийный ресурс до 1000 тыс. циклов.
- Стоимость от 600 до 1500 т.р.
С ручным, полуавтоматическим и автоматическим съёмом
С прямой, точечной и кольцевой подачей материала
Специальные виды
пресс-форм
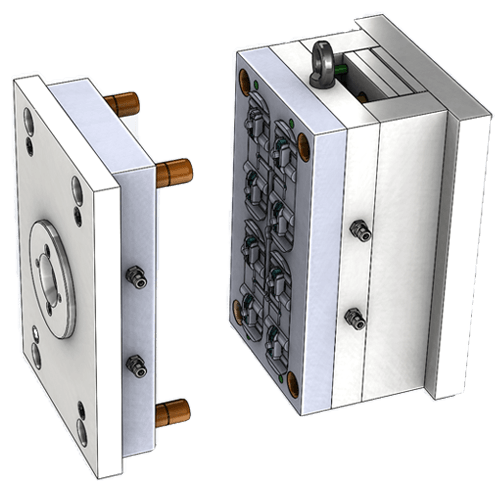
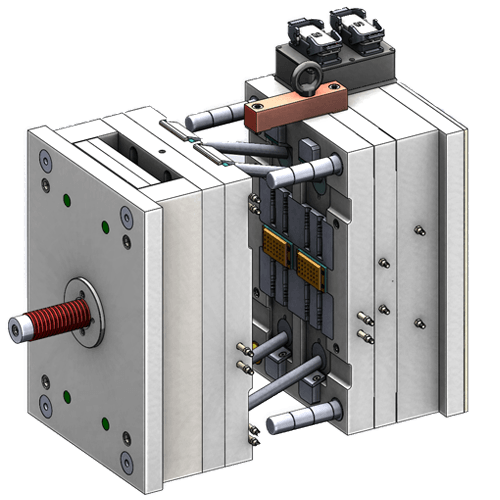
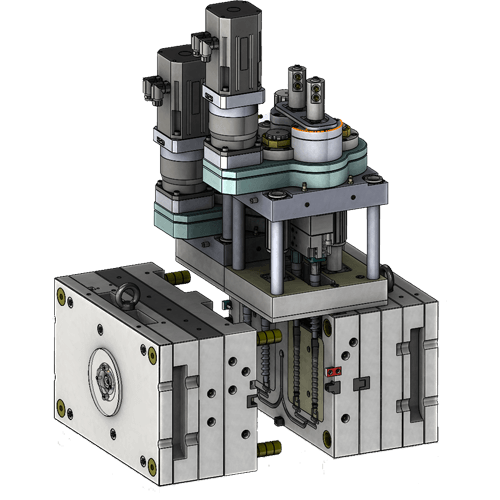
- Ручной съём – оператор извлекает изделие (для прототипов и мелких серий).
- Автоматический – изделие выталкивается и снимается роботом (для массового производства).
- Прямая (центральная) подача – расплав подаётся в центр формы.
- Точечная (боковая) подача – материал впрыскивается сбоку.
- Кольцевая подача – для симметричных деталей (например, крышек).
- Карусельные – несколько форм на вращающейся платформе (для ускорения цикла).
- Многокомпонентные – позволяют лить изделия из разных материалов за один цикл.
- С выдвижными сердечниками – для деталей с поднутрениями.
Этапы производства
01 Проектирование
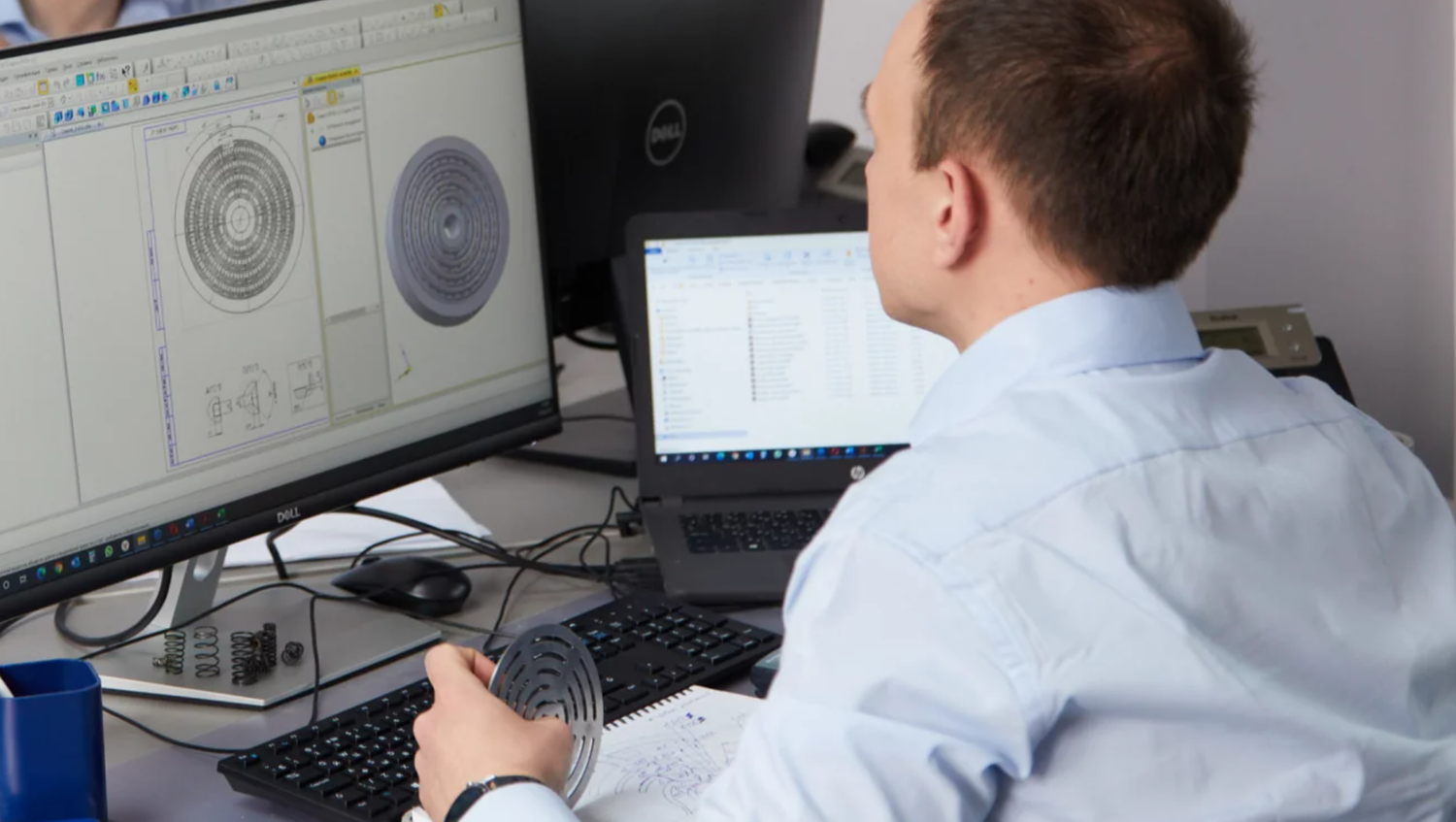
02 Выбор материалов
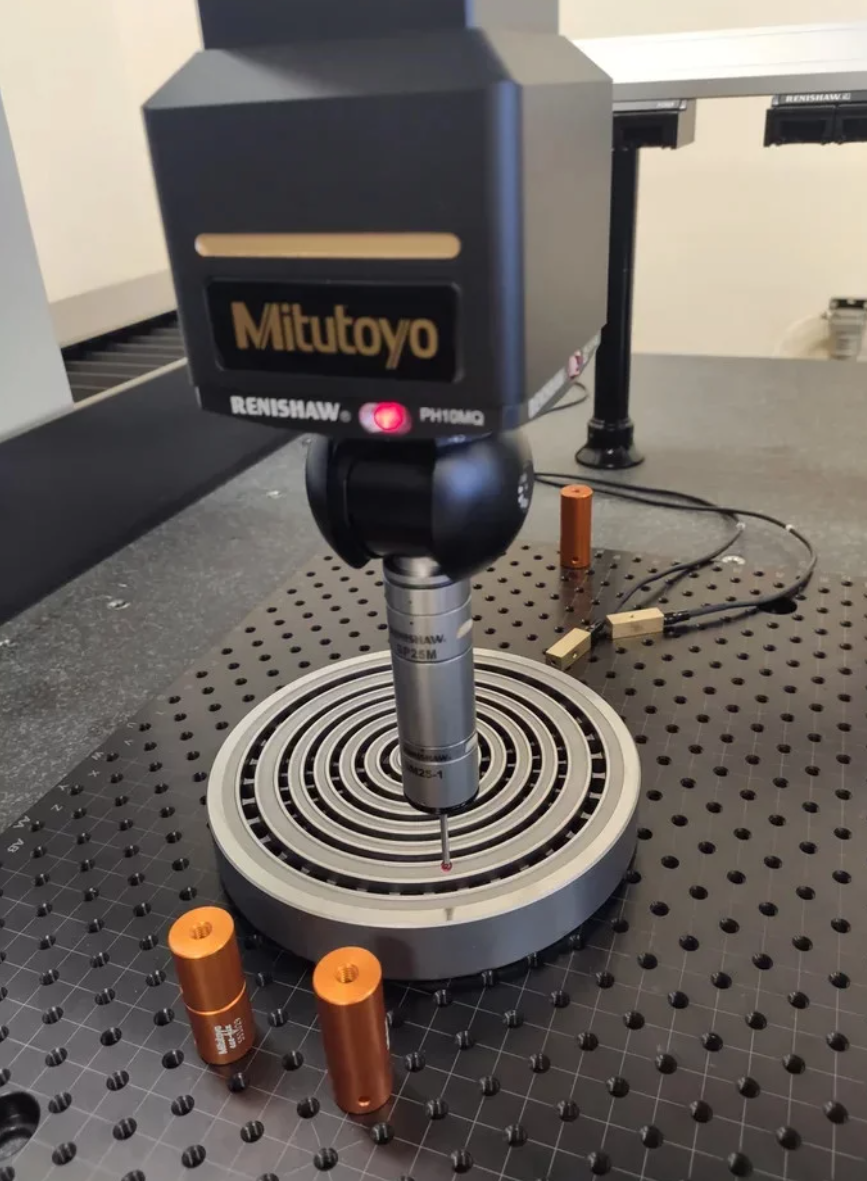
04 Сборка и испытания
05 Серийное производство
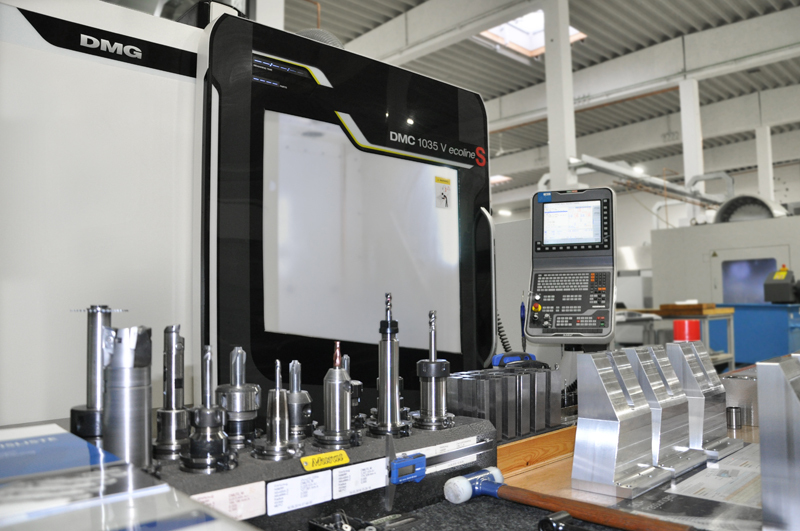
Специальные технологии производства
- | TiN (нитрид титана) | Увеличение стойкости в 2–3 раза | Для абразивных пластиков (PA+GF) |
- | DLC (алмазоподобное) | Низкий коэффициент трения | Для прецизионных форм |
- | PTFE (тефлон) | Антиадгезионные свойства | Для литья резины и силикона |
Материал и ресурс
- P20 (1.2311, 3Cr2Mo) | Стандартные пресс-формы для литья ПП, ABS, PE | Хорошая обрабатываемость, подходит для средних тиражей (50–100 тыс. циклов)
- H13 (1.2344, 4Cr5MoSiV1) | Для высоких температур (PC, POM, PA) | Термостойкость, высокая износостойкость (до 500 тыс. циклов)
- 420 (1.2083, 3Cr13) | Прозрачные пластики (PMMA, PET) | Высокая полируемость, коррозионная стойкость
- S7 (1.2363) | Ударопрочные формы | Для жестких условий (стеклонаполненные пластики)
- NAK80 (1.2738) | Высокополируемые пресс-формы | Для зеркальных поверхностей (оптика, линзы)
- Используются для высокоабразивных пластиков (с добавками стекловолокна, минералов).
- Покрытия: TiN, TiAlN, DLC (увеличивают стойкость в 2–5 раз).
- Прототипирование, мелкие серии (до 10 тыс. циклов).
- Плюсы: Легкость обработки, высокая теплопроводность.
- Минусы: Низкая износостойкость.
- Литниковая система | H13, инструментальная сталь
- Толкатели | Закалённая сталь (SKD61, 1.2343)
- Направляющие колонны | Цементированная сталь (SUJ2)
- Уплотнительные кольца | Фторопласт, термостойкая резина
Остались вопросы?
Мы готовы ответить на них.
Заполните форму обратной связи, указав все необходимые данные и ваш вопрос.
- г. Москва, проспект Маршала Жукова, д.2 стр.2, 603, 123308
- г. Москва, поселение Краснопахорское, квартал № 171