Штампы последовательного действия
«Штамп — это застывшая логика производства: каждая его деталь должна работать, а не просто существовать» Эффективный штамп — это продуманная система, где нет лишних элементов. Простота, надежность и минимализм в конструкции сокращают затраты и повышают срок службы.
Безупречный результат штамповки зависит не только от материала и оборудования, но и от грамотного проектирования. Ошибки в расчетах или экономия на оснастке обходятся дороже, чем кажется.
Внедрение автоматизации, цифровых двойников и прецизионных материалов не самоцель, а инструмент. Главное — чтобы каждый цикл штампа приносил прибыль, а не проблемы.
ЧТО МЫ ПРОИЗВОДИМ
Штамп для вырубки и пробивки
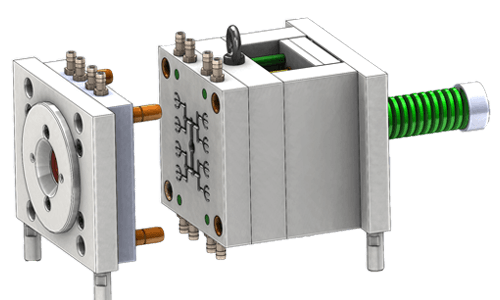
- Назхначение: Выполняет вырубку внешнего контура детали и пробивку отверстий за один цикл.
- Преимущества: Высокая точность, минимизация брака, сокращение времени производства.
- Применение: Изготовление металлических пластин, электронных компонентов, деталей корпусов.
- Изготавливаются из сталей не требующих термической обработки.
- Срок изготовления 3-5 недель.
- Гарантийный ресурс до 300 тыс. циклов.
- Стоимость от 300 до 500 т. р.
Штамп для гибки и формовки
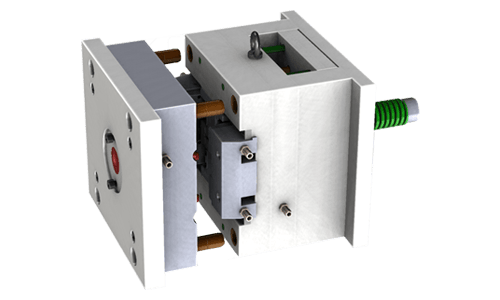
- Назначение: Последовательно выполняет гибку и формовку заготовки без переустановки.
- Преимущества: Снижение трудозатрат, сохранение геометрии детали.
- Применение: Производство кронштейнов, крепежных элементов, корпусных деталей.
- Подвижные элементы подвергаются термической обработке.
- Срок изготовления 8-10 недель.
- Гарантийный ресурс до 1000 тыс. циклов.
- Стоимость от 500 до 1000 т.р.
Штамп для вытяжки и обжима
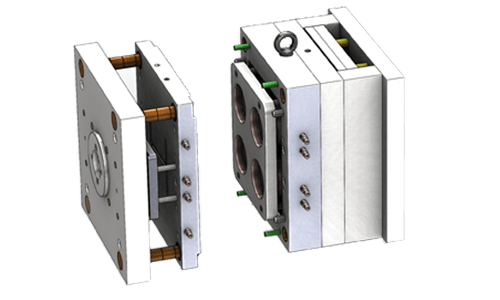
- Назначение: Используется для глубокой вытяжки с последующим обжимом кромок.
- Преимущества: Возможность создания сложных объемных деталей.
- Применение: Изготовление стаканов, крышек, корпусов приборов.
- Все формообразующие элементы и механизмы подвергаются термической обработке.
- Срок изготовления 8-12 недель.
- Гарантийный ресурс до 1000 тыс. циклов.
- Стоимость от 600 до 1500 т.р.
Комбинированный штамп для резки и чеканки
Штамп для последовательной вырубки с отходом
Штамп для прецизионной штамповки микроэлементов
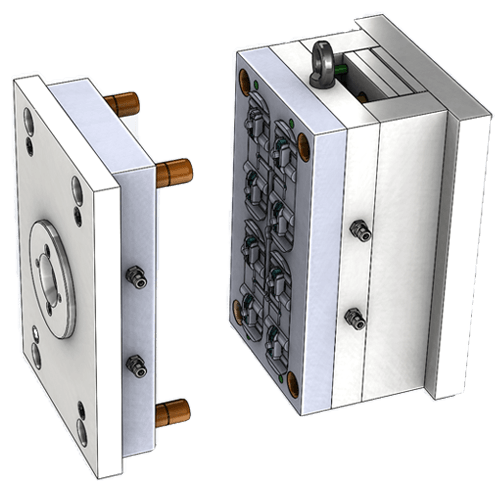
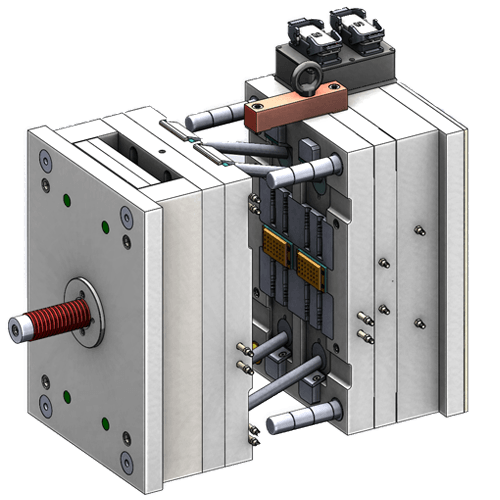
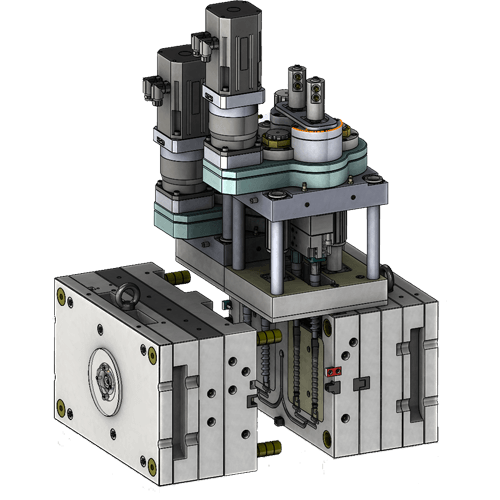
- Назначение: Сочетает вырубку с последующей чеканкой или нанесением рельефа.
- Преимущества: Экономия времени, высокая детализация рисунка.
- Применение: Производство монет, декоративных элементов, табличек.
- Все формообразующие элементы и механизмы подвергаются термической обработке.
- Срок изготовления 10-12 недель.
- Гарантийный ресурс до 1500 тыс. циклов.
- Стоимость от 800 до 1500 т.р.
- Назначение: Поэтапная вырубка детали с автоматическим удалением отходов.
- Преимущества: Уменьшение нагрузки на пресс, повышение качества кромок.
- Применение: Массовое производство мелких деталей (шайбы, прокладки).
- Все формообразующие элементы и механизмы подвергаются термической обработке.
- Срок изготовления 12-16 недель.
- Гарантийный ресурс до 2000 тыс. циклов.
- Стоимость от 1000 до 3000 т.р.
- Назначение: Изготовление миниатюрных деталей с высокой точностью.
- Преимущества: Микронные допуски, возможность работы с тонкими материалами.
- Применение: Электроника, медицинские приборы, точная механика.
- Все формообразующие элементы и механизмы подвергаются термической обработке.
- Срок изготовления 8-12 недель.
- Гарантийный ресурс до 1000 тыс. циклов.
- Стоимость от 600 до 1500 т.р.
Преимущества штампов последовательного действия
✔ Сокращение количества операций
✔ Повышение точности и повторяемости
✔ Увеличение производительности
✔ Снижение себестоимости производства
Этапы производства
Изготовление штампов – сложный технологический процесс, требующий высокой точности и соблюдения всех норм. Мы используем современное оборудование и проверенные методики, чтобы создавать надежные и долговечные инструменты.
01 Описание
Проектирование штампа последовательного действия начинается с тщательной проработки технического задания (ТЗ) и создания точной модели изделия. Это фундаментальный этап, от которого зависит точность и эффективность всего последующего производства.
Ключевые задачи этапа:
1. Сбор исходных данных:
- Получение чертежей детали от заказчика (2D/3D) или образца для обмеров
- Определение материала заготовки (марка стали, алюминий, медь и др.)
- Уточнение толщины материала и требуемой точности обработки
2. Анализ технологичности детали:
- Проверка возможности изготовления штамповочным методом
- Выявление сложных элементов (узкие перемычки, глубокие вытяжки)
- Оценка необходимой последовательности операций
3. Разработка технического задания:
- Определение типа штампа (последовательный, с вырубкой-гибкой и т.д.)
- Расчет примерного усилия пресса
- Выбор оборудования для производства
4. Создание 3D-модели изделия:
- Детальное моделирование в CAD-системах (SolidWorks, КОМПАС-3D)
- Проверка на технологические ограничения
- Экспорт модели для последующих расчетов
Результаты этапа:
✅ Утвержденное техническое задание на проектирование
✅ Точная 3D-модель будущей детали
✅ Определенные требования к точности и качеству поверхности
✅ Предварительная оценка сложности и сроков проекта
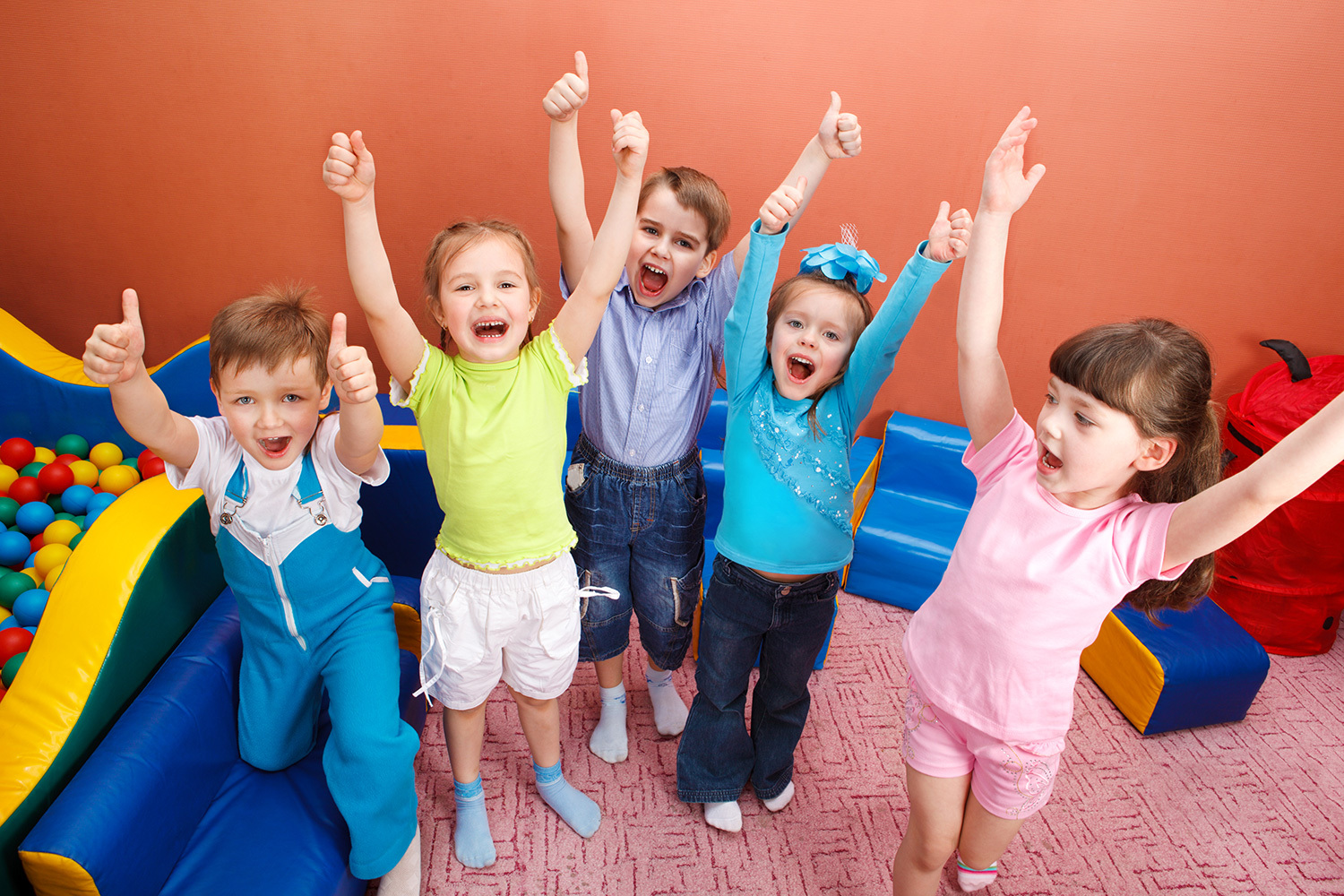
Ключевые моменты разработки и проектирования
- Анализ ТЗ – изучение чертежей детали, требований к материалу, точности и производительности.
- 3D-моделирование (в SolidWorks, AutoCAD, КОМПАС) – создание виртуальной модели штампа с учетом кинематики работы.
- Расчет усилий – определение необходимого давления пресса, выбор оптимального хода.
- Разработка технологического процесса – последовательность операций (вырубка, гибка, формовка, отрезка).
- Проектирование оснастки – конструкция матрицы, пуансона, направляющих, системы удаления отходов.
Срок выполнения: 3-7 рабочих дней в зависимости от сложности детали
Разработка технологического процесса и схемы раскроя
После утверждения технического задания и модели изделия мы переходим к ключевому этапу – созданию оптимального технологического процесса и схемы раскроя материала. Это определяет эффективность всего производства и экономическую целесообразность штампа.
Основные работы этапа:
1. Разработка последовательности операций:
- Детальный анализ геометрии изделия
- Определение порядка выполнения операций (вырубка, пробивка, гибка, формовка)
- Расчет необходимого количества позиций в штампе
2. Проектирование схемы раскроя:
- Оптимизация расположения деталей на полосе/ленте
- Расчет коэффициента использования материала (КИМ)
- Определение ширины перемычек и технологических припусков
3. Технико-экономическое обоснование:
- Сравнение различных вариантов раскроя
- Расчет себестоимости с учетом отходов производства
- Выбор наиболее экономичного решения
4. Моделирование подачи материала:
- Разработка системы позиционирования заготовки
- Проектирование механизмов подачи (роликовых, клещевых)
- Проверка кинематики в специализированном ПО
Используемое программное обеспечение:
- AutoForm – для симуляции процессов штамповки
- Logopress – для проектирования раскроя
- 3D CAD системы – для визуализации процесса
Результаты этапа:
✅ Утвержденная схема раскроя с максимальным КИМ
✅ Технологическая карта с последовательностью операций
✅ 3D-модель подачи материала
✅ Расчет экономической эффективности
Особенности нашего подхода:
- Используем современные системы 3D-моделирования
- Проводим виртуальный анализ штампуемости
- Предлагаем оптимизацию конструкции для снижения себестоимости
- Обеспечиваем полное соответствие ГОСТ и ISO
Срок выполнения этапа: от 1 до 5 рабочих дней в зависимости от сложности детали
Преимущества нашей разработки:
- Минимизация отходов (до 15% экономии материала)
- Оптимальное количество технологических переходов
- Учет особенностей оборудования заказчика
- Возможность последующей модернизации
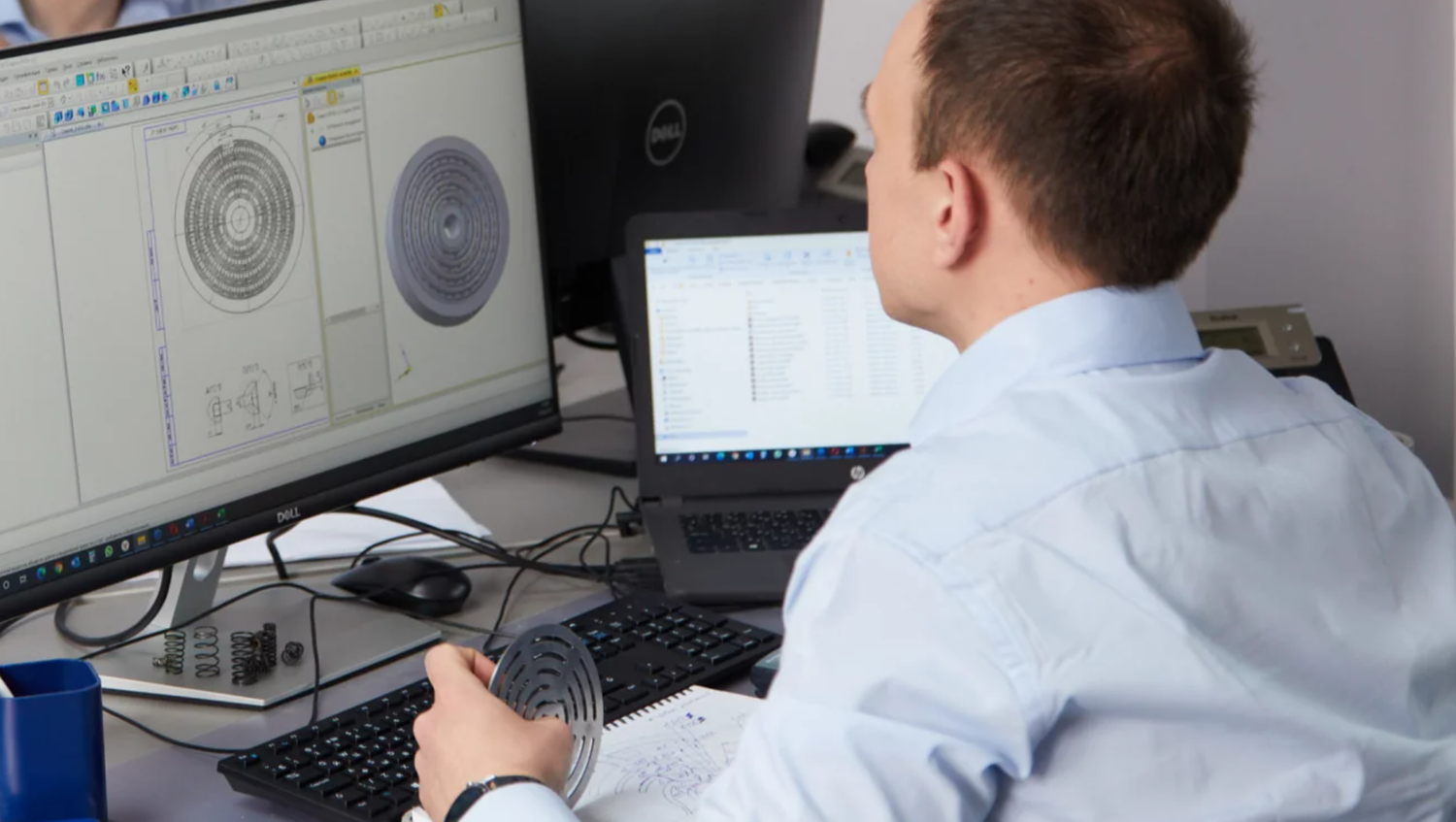
Как заказать проектирование штампа?
1. Пришлите чертеж детали или образец.
2. Мы выполним расчеты и предложим оптимальную конструкцию.
3. Согласуем техническое решение и сроки.
4. Изготовим штамп и проведем испытания.
Гарантируем качество и соответствие ГОСТ, ISO!
2. Изготовление оснастки (50% стоимости)**
- **Матрицы/пуансоны:**
- Механообработка (фрезеровка, шлифовка)
- Электроэрозия (ЭЭР, проволочная резка)
- Термообработка (закалка, отпуск до HRC 58-62)
- Направляющие: прецизионные шариковые втулки
- Системы удаления отходов / выталкивания деталей
*Материалы: Х12МФ, твердые сплавы, керамика для микроштамповки.*
Преимущества нашего проектирования
✔ Минимизация отходов – оптимизированный раскрой снижает себестоимость.
✔ Высокая точность – компьютерное моделирование исключает ошибки.
✔ Долговечность – правильный подбор материалов увеличивает ресурс.
✔ Гибкость – возможность модернизации под новые задачи.
02 Проектирование
Проектирование штампов последовательного действия – ключевой этап в создании точного и долговечного инструмента для металлообработки. Наши инженеры разрабатывают штампы с учетом всех технологических требований, обеспечивая высокую производительность и минимальный процент брака.
Основные этапы проектирования
1. Анализ технического задания
- Изучение чертежей детали и требований заказчика.
- Определение материала заготовки, толщины, точности обработки.
- Выбор оптимального количества операций в одном ходе пресса.
2. Разработка 3D-модели и схемы раскроя
- Создание цифровой модели штампа в CAD-системах (SolidWorks, AutoCAD, КОМПАС).
- Оптимизация раскроя металла для минимизации отходов.
- Расчет усилий деформации и нагрузок на элементы штампа.
3. Конструкция штампа
- Разработка матриц и пуансонов для каждой операции (вырубка, гибка, пробивка).
- Проектирование направляющих систем для точного позиционирования заготовки.
- Расчет зазоров между рабочими частями для предотвращения заклинивания.
- Выбор механизма удаления отходов (отсечка, продувка, лотки).
4. Моделирование процессов штамповки
- Проверка кинематики в CAE-программах (AUTOFORM, DEFORM).
- Анализ возможных дефектов (складки, трещины, перекосы).
- Корректировка конструкции для улучшения качества детали.
5. Подбор материалов и термообработки
- Матрицы и пуансоны – легированные стали (Х12МФ, 6ХВ2С) с закалкой до HRC 58-62.
- Направляющие – износостойкие сплавы с твердым хромированием.
- Основание штампа – сталь 45 или сталь 40Х для устойчивости к нагрузкам.
6. Подготовка рабочей документации
- Чертежи всех компонентов с допусками и шероховатостью.
- Технологическая карта сборки и наладки.
- Инструкция по эксплуатации и обслуживанию.
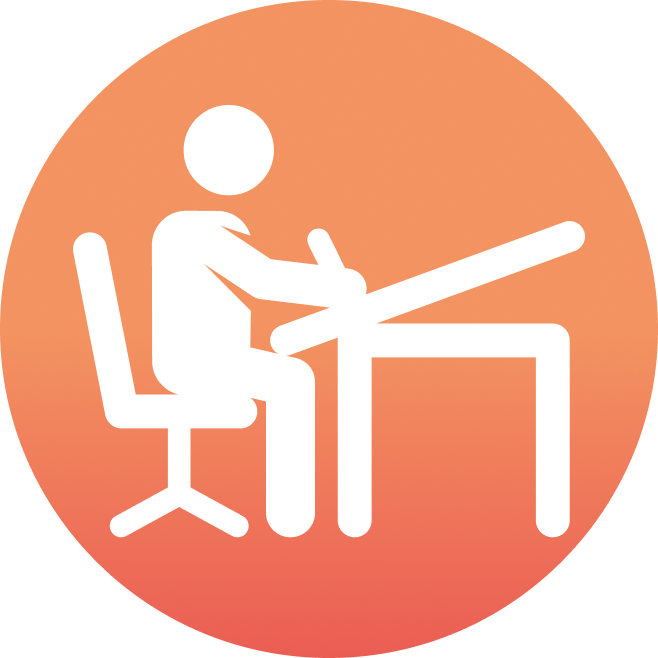
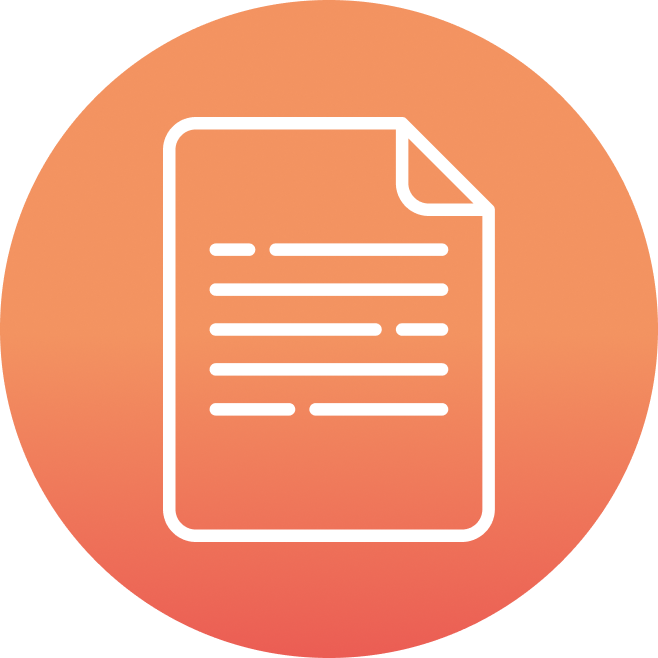
03 Изготовление продукции
Этап изготовления деталей штампа
После завершения проектирования начинается ключевой этап производства – изготовление деталей штампа. Мы используем современное оборудование с ЧПУ и строгий контроль качества на каждом этапе, чтобы обеспечить высокую точность и долговечность инструмента.
Основные этапы изготовления
1. Подготовка материалов
- Выбор заготовок:
- Матрицы и пуансоны – инструментальные стали (Х12МФ, 6ХВ2С)
- Направляющие – закаленные стали с износостойкими покрытиями
- Основание – конструкционные стали (40Х, 45)
- Контроль качества металла: проверка сертификатов, ультразвуковой контроль
2. Механическая обработка
- Фрезерная обработка на станках с ЧПУ:
- Черновая обработка с припуском под термообработку
- Чистовая обработка ответственных поверхностей
- Токарные работы: изготовление втулок, осей, крепежных элементов
- Сверление и расточка: точные отверстия под направляющие
3. Термическая обработка
- Закалка: нагрев до критических температур с последующим охлаждением
- Отпуск: для снятия внутренних напряжений
- Проверка твердости: контроль по шкале HRC (58-62 для рабочих элементов)
4. Финишная обработка
- Шлифовка: точная обработка рабочих поверхностей
- Плоскошлифовальные станки – для матриц и плит
- Круглошлифовальные – для пуансонов и втулок
- Электроэрозионная обработка (ЭЭРО):
- Проволоко-вырезные станки – для сложных контуров
- Прошивные – для глухих отверстий и пазов
- Притирка и полировка: для уменьшения трения
5. Контроль качества
- Измерение геометрии:
- Координатно-измерительные машины (КИМ)
- Оптические профилометры
- Проверка зазоров: между матрицей и пуансоном
- Тестовый прогон: на эталонных заготовках
Изготовление составных частей штампа
- Матрицы и пуансоны – фрезерование, токарная обработка, шлифовка.
- Направляющие элементы – точная обработка для минимизации люфтов.
- Детали крепления – изготовление плит, втулок, фиксаторов.
3. Термическая обработка и упрочнение
- Закалка, отпуск, цементация для повышения износостойкости.
- Проверка твердости (HRC) на каждом критичном узле.
3. Сборка и юстировка**
- Механическая подгонка всех компонентов
- Проверка зазоров (0,05–0,1 мм для тонколистовой стали)
- Тестовая штамповка на эталонных заготовках
*Критерий: первые 10 деталей должны соответствовать чертежу.*
Используемое оборудование
✔ Фрезерные центры с ЧПУ (DMG Mori, Haas)
✔ Прецизионные шлифовальные станки (Okamoto, Walter)
✔ Электроэрозионные станки (AgieCharmilles, Mitsubishi)
✔ Контрольно-измерительные системы (Zeiss, Mitutoyo)
Преимущества нашего производства
✅ Точность до 0,005 мм для критичных элементов
✅ Собственный парк станков – полный цикл без субподряда
✅ Соблюдение сроков благодаря отработанным процессам
✅ Гарантия на все детали
Срок изготовления: от 10 рабочих дней (зависит от сложности штампа)
Следующий этап: Сборка и испытания штампа
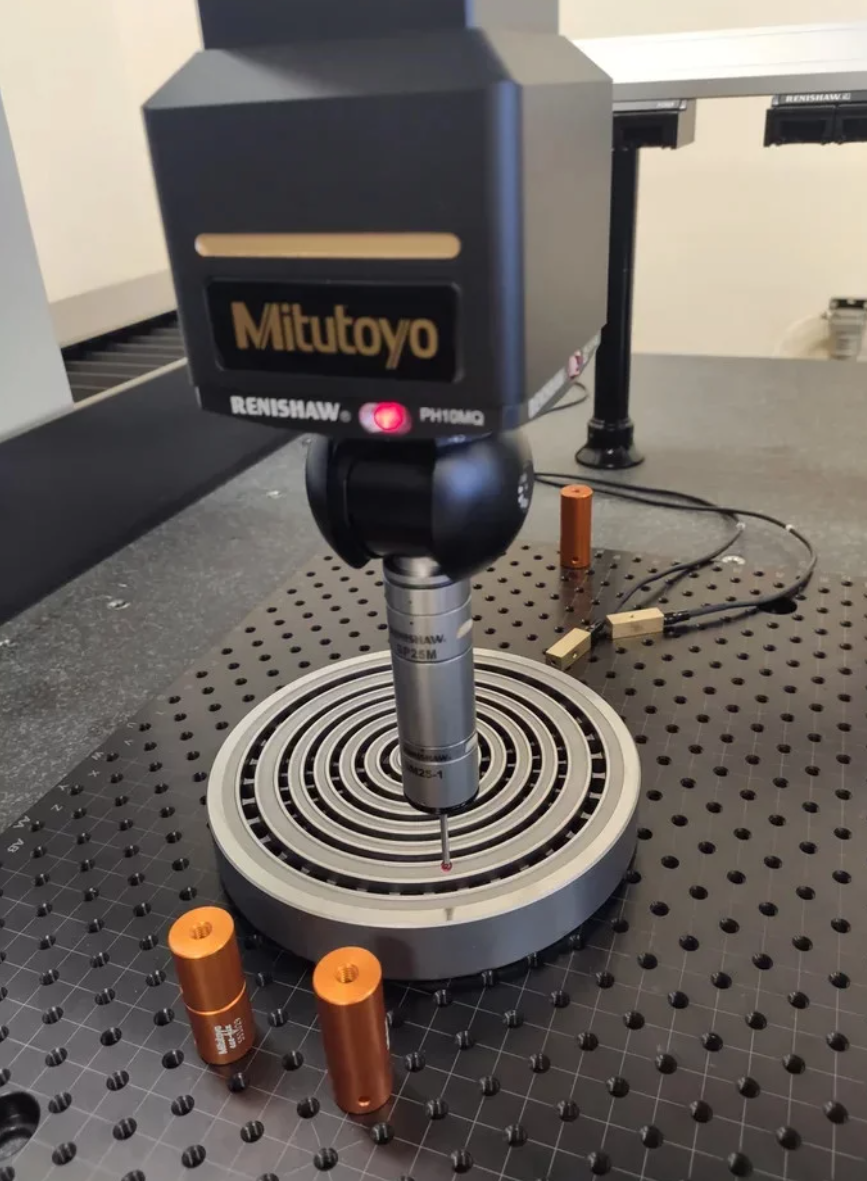
4. Пуско-наладка на производстве**
- Установка на пресс, подключение автоматики
- Настройка подачи (лента, робот-манипулятор)
- Корректировка параметров (усилие, скорость, ход)
*Важно: обучение оператора работе с оснасткой.*
4. Сборка и подгонка
- Механическая сборка с проверкой соосности и зазоров.
- Доводка рабочих поверхностей (притирка, полировка).
5. Испытания и доводка
- Пробная штамповка на производственном прессе.
- Корректировка геометрии при необходимости.
- Контроль качества готовых деталей.
6. Поставка и ввод в эксплуатацию
- Шеф-монтаж и настройка на оборудовании заказчика.
- Обучение персонала.
- Гарантийное и постгарантийное обслуживание.
Критерии успешных испытаний
✔ Деталь соответствует чертежу (допуски ±0,1 мм)
✔ Отсутствие дефектов на заготовке (замины, трещины)
✔ Стабильная работа в автоматическом режиме
✔ Ресурс штампа – не менее 500 000 циклов
Наши преимущества
✅ Собственная испытательная база – прессы до 300 тонн
✅ Видеофиксация испытаний для прозрачности процесса
✅ Гарантия на настройку – бесплатные корректировки в течение 6 месяцев
✅ Обучение операторов работе со штампом
Сроки: 3–5 рабочих дней на сборку и испытания
Этот раздел можно дополнить:
- Видео процесса испытаний
- Примеры отчетов по испытаниям
- Отзывы клиентов о качестве сборки
- Сравнение до/после корректировок
Следующий этап: Поставка и ввод в эксплуатацию
04 Испытания
Этап сборки и испытаний штампа
После изготовления всех деталей начинается ответственный этап сборки и тестирования штампа. Этот процесс гарантирует точность работы инструмента и соответствие техническим требованиям заказчика.
Основные этапы сборки и испытаний
1. Подготовка к сборке
- Комплектация деталей: проверка наличия всех элементов согласно спецификации
- Очистка поверхностей: удаление следов обработки и загрязнений
- Подготовка оснастки: проверка крепежа, направляющих, пружин
2. Механическая сборка
- Установка матриц и пуансонов: точная фиксация в корпусе штампа
- Монтаж направляющих систем: обеспечение плавного хода
- Регулировка зазоров: между рабочими элементами (0,05–0,1 мм в зависимости от материала)
- Установка выталкивателей и систем удаления отходов
3. Предварительные проверки
- Контроль соосности: всех подвижных частей
- Проверка хода: плавность работы, отсутствие заклинивания
- Тест на холостом ходу: имитация работы без заготовки
4. Испытания на производственном прессе
- Пробная штамповка:
- Использование эталонного материала
- Постепенное увеличение нагрузки
- Контроль качества деталей:
- Проверка геометрии (штангенциркули, микрометры)
- Анализ состояния кромок (отсутствие заусенцев, трещин)
- Корректировка (при необходимости):
- Доводка рабочих поверхностей
- Регулировка усилия выталкивателей
5. Финализация и подготовка к передаче
- Окончательная регулировка: всех механизмов
- Смазка трущихся частей: для увеличения ресурса
- Упаковка: защита от повреждений при транспортировке
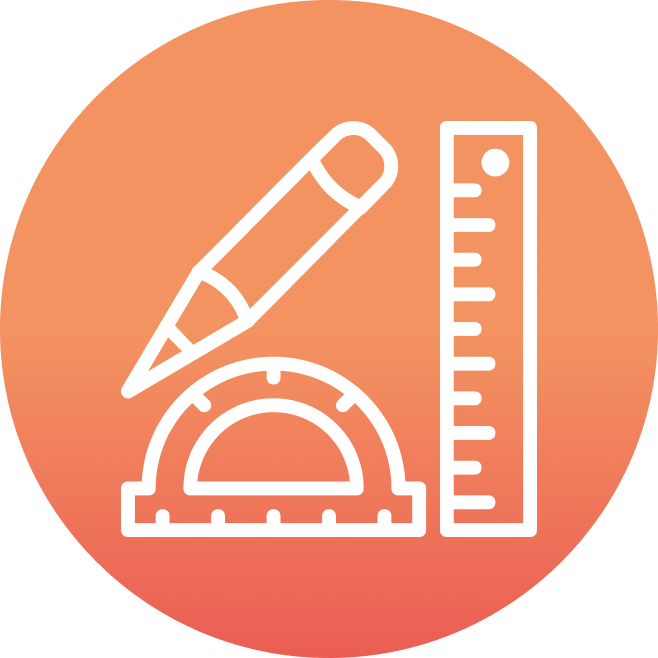
Замеры
Осуществлению замеров детали с помощью координатно-измерительной машины (КИМ) Mitutoyo (пр-во. Япония).
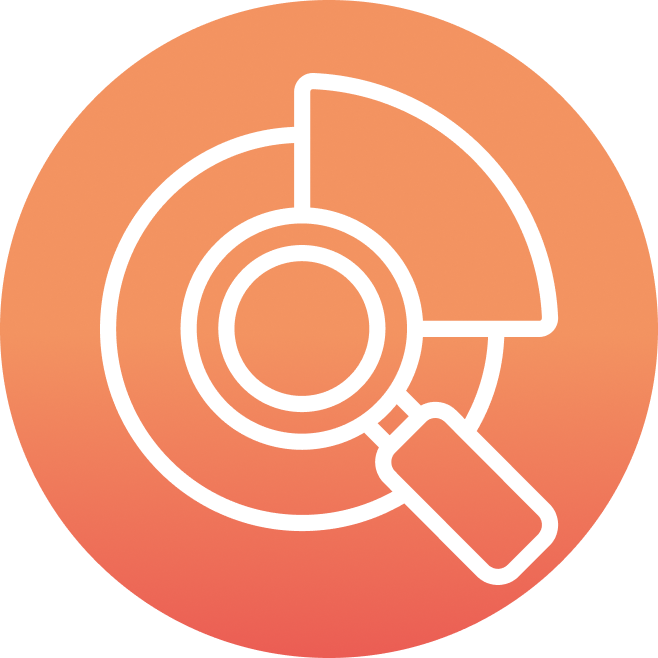
Исследование
Выполненяем ультразвуковой контроль (УЗК) и цветную дефектоскопию (ЦД). Определяем химический состав материала с помощью спектрального анализа, а так же его твердость.
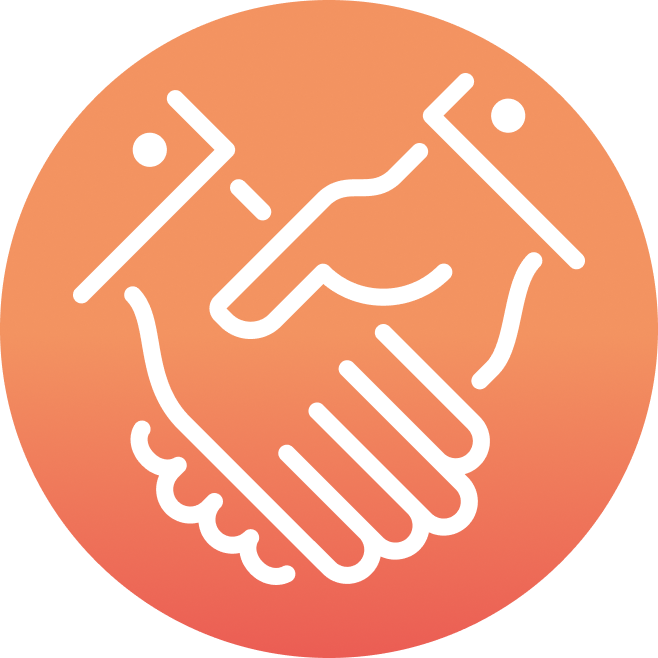
Заключение
По окончанию выполненных работ Заказчику передается заключение с предоставлением результатов проведенных замеров и испытаний.
05 Гарантийное обслуживание
Поставка, ввод в эксплуатацию и гарантийное обслуживание
После успешных испытаний штамп готов к передаче заказчику. Мы обеспечиваем профессиональный ввод оборудования в эксплуатацию и дальнейшее сопровождение, чтобы гарантировать его бесперебойную работу.
Процесс поставки и ввода в эксплуатацию
1. Организация поставки
- Безопасная упаковка:
- Жесткая деревянная обрешетка
- Антикоррозийная обработка рабочих поверхностей
- Маркировка хрупких элементов
- Транспортировка:
- Собственный автотранспорт (по РФ)
- Организация ж/д или авиаперевозок (для международных заказчиков)
- Таможенное оформление (при необходимости)
2. Шеф-монтаж и пусконаладка
- Монтаж на пресс:
- Проверка совместимости оборудования
- Юстировка по уровню
- Подключение систем смазки и охлаждения
- Настройка параметров:
- Регулировка хода ползуна
- Установка оптимального усилия
- Тестовая прогонка первых 50-100 деталей
3. Обучение персонала
- Теоретическая часть:
- Принцип работы штампа
- Правила безопасности
- Особенности обслуживания
- Практика:
- Замена изнашиваемых элементов
- Регулировка в процессе работы
- Диагностика неисправностей
Гарантийное и постгарантийное обслуживание
Гарантийные обязательства
- Срок гарантии: 12 месяцев с момента ввода в эксплуатацию
- Бесплатные услуги:
- Выезд специалиста при неисправностях
- Замена дефектных деталей
- Консультации по оптимизации работы
Постгарантийное обслуживание
- Ремонт и модернизация:
- Восстановление геометрии рабочих поверхностей
- Замена изношенных матриц/пуансонов
- Адаптация под новые материалы
- Сервисные пакеты:
| Пакет | Описание | Сроки реагирования |
|---|---|--|
| Стандарт | Плановые осмотры 2 раза в год | 5 рабочих дней |
| Премиум | Круглосуточная поддержка + аварийный выезд | 24 часа |
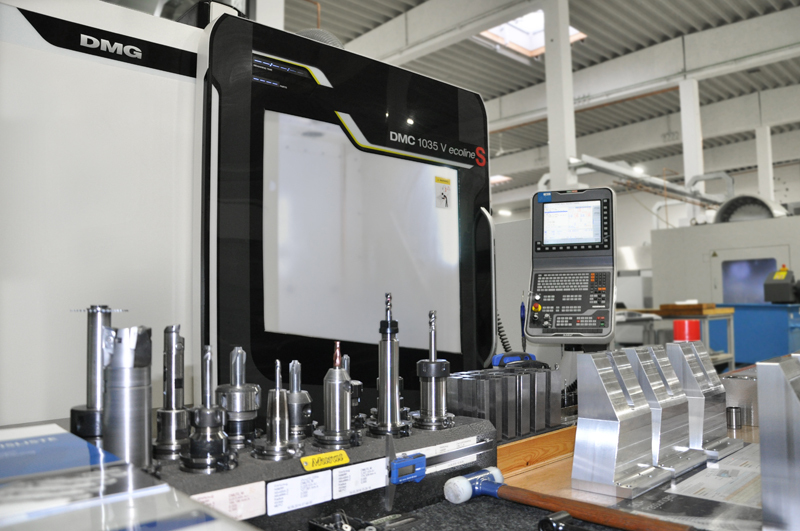
4. Пуско-наладка на производстве**
- Установка на пресс, подключение автоматики
- Настройка подачи (лента, робот-манипулятор)
- Корректировка параметров (усилие, скорость, ход)
*Важно: обучение оператора работе с оснасткой.*
4. Сборка и подгонка
- Механическая сборка с проверкой соосности и зазоров.
- Доводка рабочих поверхностей (притирка, полировка).
5. Испытания и доводка
- Пробная штамповка на производственном прессе.
- Корректировка геометрии при необходимости.
- Контроль качества готовых деталей.
6. Поставка и ввод в эксплуатацию
- Шеф-монтаж и настройка на оборудовании заказчика.
- Обучение персонала.
- Гарантийное и постгарантийное обслуживание.
5. Мониторинг и обслуживание**
- Регулярная замена изношенных компонентов (пуансоны, матрицы)
- Контроль качества деталей (раз в 500–1000 циклов)
- Ведение журнала износа для прогнозирования ремонта
*Срок службы штампа: 200 000–1 000 000 циклов в зависимости от материала.*
Логистика обслуживания
- Диагностика онлайн: передача данных через IoT-датчики (для премиум-клиентов)
- Склад расходников: хранение резервных деталей у заказчика (по договору)
- Срочное изготовление: повторение утраченных элементов по исходным 3D-моделям
Почему клиенты выбирают нас?
✔ Собственная сервисная служба – 15 инженеров в разных регионах
✔ Прозрачная отчетность: фото/видео фиксация всех работ
✔ Гибкие условия: обслуживание по факту или абонемент
✔ Архив проектов: пожизненное хранение документации для повторных заказов
Специальные технологии производства
4. Аддитивные технологии
- 3D-печать пресс-форм
- Быстрое прототипирование сложных элементов
- Использование металлических порошков (мартенситные стали)
- Гибридное производство
- Комбинация 3D-печати с механической обработкой
5. Ионно-плазменное напыление
- Нанесение защитных покрытий
- TiN, TiAlN – для увеличения стойкости к абразивному износу
- DLC (алмазоподобный углерод) – для штамповки алюминия
Контроль качества на всех этапах
| Технология | Применение | Точность |
|---|---|---|
| 3D-сканирование | Сравнение с CAD-моделью | ±0,01 мм |
| Координатные измерения | Проверка геометрии | ±0,002 мм |
| Ультразвуковая дефектоскопия | Выявление внутренних дефектов | Глубина до 200 мм |
Преимущества наших технологий
✅ Снижение времени производства на 20-40% за счет комбинированных методов
✅ Уникальные решения для штамповки высокопрочных материалов
✅ Экологичность: минимальное использование СОЖ за счет сухой обработки
✅ Цифровой двойник каждого штампа для прогнозирования износа
Проектирование
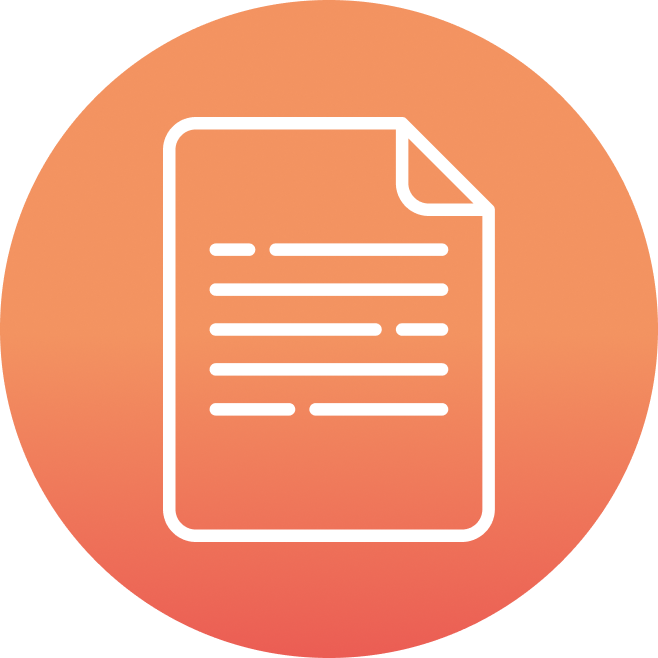
Наше производство использует передовые методы обработки, которые обеспечивают высочайшую точность, износостойкость и долговечность штампов. Мы внедряем инновационные решения для сложных задач металлообработки.
Уникальные технологии в изготовлении штампов
1. Прецизионная электроэрозионная обработка (ЭЭРО)
- Проволочно-вырезные станки
- Точность реза до ±0,005 мм
- Возможность обработки закаленных сталей (HRC 60+)
- Создание сложных контуров с минимальными радиусами
- Прошивная электроэрозия
- Изготовление глухих отверстий и 3D-форм
- Минимальная шероховатость поверхности (Ra 0,2-0,4 мкм)
2. Лазерная наплавка и упрочнение
- Восстановление кромок матриц/пуансонов
- Нанесение износостойких сплавов (стеллит, карбиды вольфрама)
- Увеличение ресурса в 3-5 раз
- Локальная закалка лазером
- Точечное изменение твердости без деформации детали
3. Микрообработка ультразвуком
- Чистовая обработка ответственных поверхностей
- Достижение шероховатости Ra 0,05 мкм
- Полировка труднодоступных полостей
- Создание микротекстур
- Антифрикционные поверхности для улучшения съема деталей
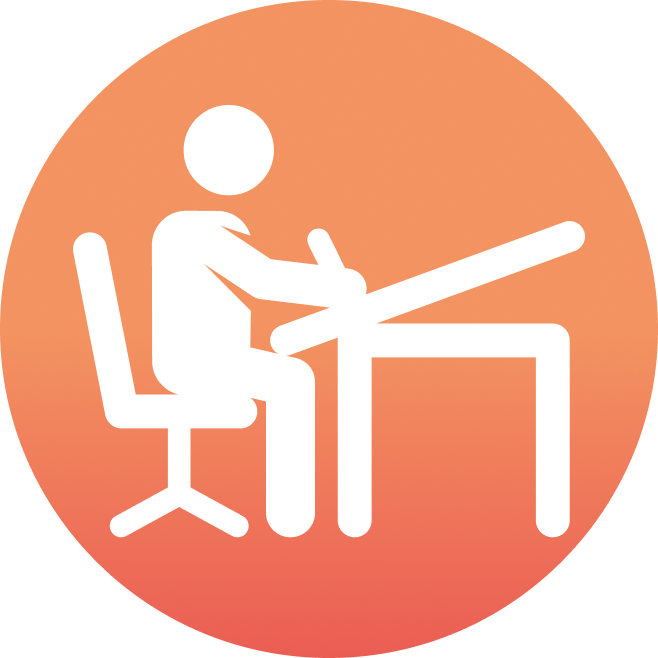
Разработка по нашим чертежам
Пример внедрения:
Для автомобильного компонента из стали DP800:
- Применили лазерную наплавку кромок → ресурс увеличился с 150 000 до 500 000 циклов
- Использовали ионное покрытие TiAlN → исключили схватывание материала
ОТРАСЛИ ПРОМЫШЛЕНОСТИ
Отрасли и применение штампов последовательного действия
Штампы последовательного действия широко используются в различных отраслях промышленности благодаря своей эффективности, точности и возможности массового производства деталей сложной формы.
Ключевые отрасли применения
1. Автомобилестроение
- Детали кузова: двери, капоты, крылья, усилители
- Элементы подвески: кронштейны, рычаги, опоры
- Тормозные системы: диски, суппорты, скобы
- Интерьер: панели приборов, кронштейны крепления
Преимущества:
✔ Высокая производительность (до 1 000 деталей в час)
✔ Минимизация отходов материала
✔ Стабильное качество при массовом производстве
2. Авиакосмическая промышленность
- Обшивка и силовые элементы: шпангоуты, стрингеры
- Детали двигателей: корпусные элементы, теплообменники
- Крепежные системы: пластины, кронштейны
Особенности:
- Работа с титановыми и алюминиевыми сплавами
- Повышенные требования к точности (±0,05 мм)
- Специальные покрытия для защиты от коррозии
3. Электроника и приборостроение
- Корпуса устройств: smartphones, ноутбуки, роутеры
- Радиаторы охлаждения: сложные ребристые структуры
- Контактные группы: разъемы, токопроводящие элементы
Технологические нюансы:
- Микроштамповка (толщина материала от 0,1 мм)
- Чистые поверхности без заусенцев
- Использование медных и бронзовых сплавов
Экономические аспекты:
- Оптимизация для крупносерийного производства
- Быстрая переналадка под разные модели
- Снижение себестоимости единицы продукции
Уникальные возможности наших штампов
- Гибкие производственные линии: быстрое переоснащение под новые задачи
- Комплексные решения: от проектирования до постгарантийного обслуживания
- Материальный инжиниринг: подбор сплавов под конкретные условия эксплуатации
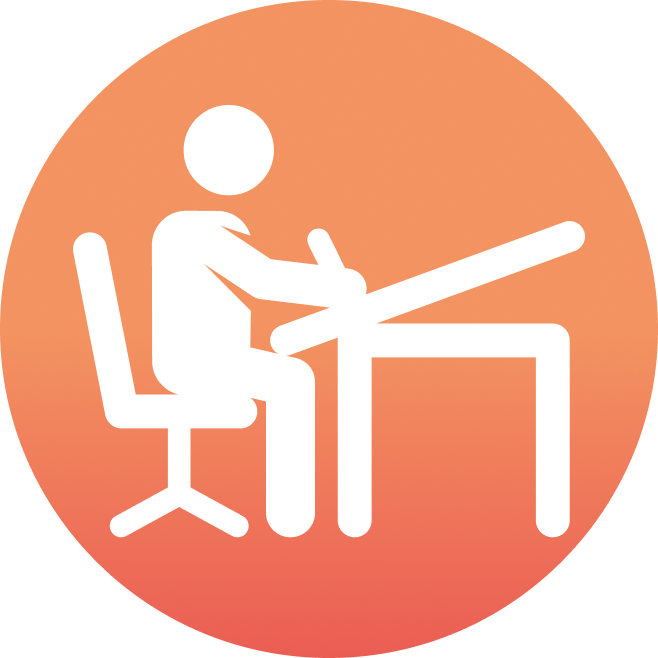
4. Энергетика и электротехника
- Лопатки турбин: профильные элементы
- Теплообменники: пластинчатые конструкции
- Корпуса трансформаторов: защитные кожухи
Критические параметры:
- Стойкость к высоким температурам
- Особые требования к электропроводности
- Защита от вибрационных нагрузок
5. Медицинская техника
- Хирургические инструменты: зажимы, скальпели
- Имплантаты: ортопедические пластины
- Корпуса аппаратуры: МРТ, рентген-оборудование
Специфика:
- Биосовместимые материалы (титан, нержавеющие стали)
- Стерилизуемые поверхности
- Микронные допуски
6. Потребительские товары
- Бытовая техника: элементы стиральных машин, холодильников
- Мебельная фурнитура: петли, крепежи
- Строительные компоненты: кровельные элементы, системы вентиляции
Пример из практики:
Для производителя электротранспорта разработали штамп для одновременной:
1. Вырубки контура аккумуляторной панели
2. Пробивки 32 отверстий под охлаждение
3. Гибки крепежных фланцев
Результат: сокращение цикла производства на 40%
Наш станочный парк
Примеры наших работ
Материалы, сертификация и ресурс
Применяемые материалы для изготовления штампов
Качество и долговечность штампов напрямую зависят от правильно подобранных материалов. Мы используем специальные инструментальные стали, твердые сплавы и защитные покрытия, чтобы обеспечить максимальный ресурс и стабильность производства.
Основные материалы для штампов
1. Инструментальные стали
Для матриц и пуансонов:
| Марка стали | Твердость (HRC) | Применение |
|------------|--------------|------------|
| Х12МФ | 58-62 | Штамповка тонколистовой стали, вырубка |
| 6ХВ2С | 56-60 | Гибка и формовка |
| Р6М5 (быстрорез) | 62-64 | Высокоскоростная штамповка |
| 9ХС | 58-61 | Универсальные штампы средней нагруженности |
Для направляющих и плит:
- Сталь 40Х (HRC 45-50) – основание штампа
- Сталь 20Х13 (HRC 50-54) – износостойкие направляющие
2. Твердые сплавы
- ВК8, ВК10 (вольфрам-кобальтовые):
- Для вырубки/пробивки абразивных материалов (стеклотекстолит, композиты)
- Ресурс в 5-7 раз выше, чем у инструментальной стали
- Т15К6 (титано-вольфрамовые):
- Штамповка нержавеющих сталей и цветных сплавов
Подбор материала под задачу
Для штамповки:
- Углеродистая сталь (08кп, 20):
- Недорогие штампы из Х12МФ или 9ХС
- Нержавеющая сталь (AISI 304):
- Твердые сплавы ВК8 + покрытие TiAlN
- Алюминий (АД31, АМг5):
- Сталь 6ХВ2С с полировкой + DLC-покрытие
Для высокоресурсных штампов:
- Комбинированная конструкция:
- Основание – сталь 40Х
- Рабочие вставки – ВК10
- Покрытие – многослойное (TiN+TiAlN)
Инновационные материалы
- Металлокерамика (cermet):
- Для микроштамповки толщиной <0,1 мм
- Порошковые стали (CPM-10V):
- Износостойкость в 3 раза выше традиционных сталей
- Поликристаллический алмаз (PCD):
- Штамповка армированных пластиков
Контроль качества материалов
1. Спектральный анализ – проверка химического состава
2. Ультразвуковая дефектоскопия – выявление внутренних дефектов
3. Микротвердомер – измерение HRC в разных зонах
Почему важно правильное материаловедение?
✔ Экономия: Подбор оптимального материала сокращает затраты на 15-30%
✔ Ресурс: Грамотный выбор увеличивает срок службы в 2-5 раз
✔ Качество: Исключает брак из-за преждевременного износа
Пример:
Для клиента из автопрома:
- Заменили Х12МФ на ВК10 с TiN-покрытием
- Ресурс штампа вырос с 200 000 до 1 000 000 циклов
- Себестоимость детали снизилась на 22%
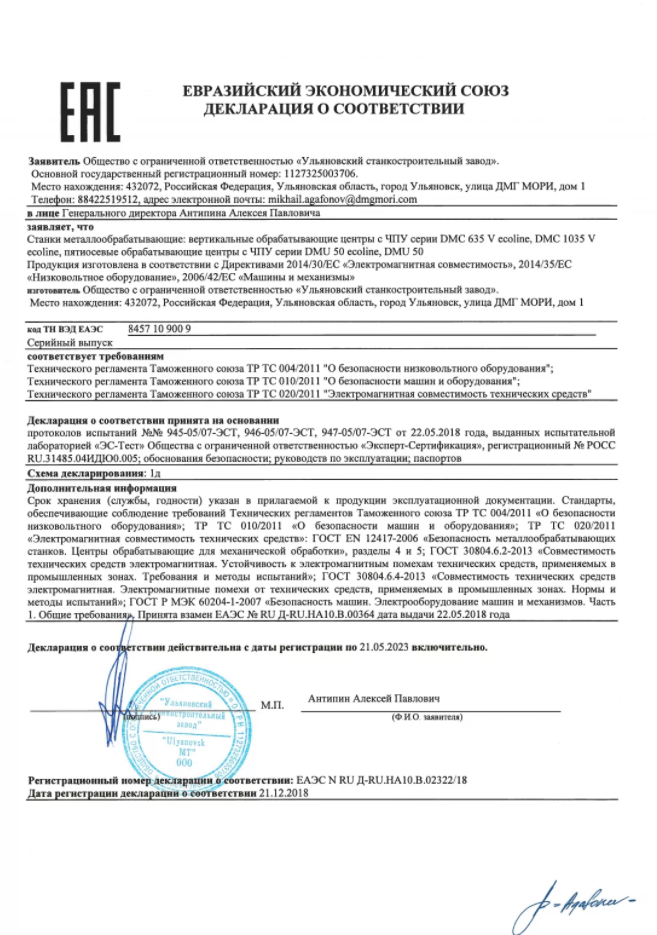
Защитные покрытия
| Покрытие | Метод нанесения | Эффект |
| TiN (нитрид титана) | PVD-вакуумное напыление | Увеличение стойкости к истиранию |
| TiAlN (алюмо-нитрид титана) | Ионно-плазменное | Термостойкость до 800°C |
| DLC (алмазоподобный углерод) | CVD-осаждение | Антифрикционное для алюминия и меди |
Остались вопросы?
Мы готовы ответить на них.
Заполните форму обратной связи, указав все необходимые данные и ваш вопрос.
Офис
- г. Москва, проспект Маршала Жукова, д.2 стр.2, 603, 123308
Производство
- г. Москва, поселение Краснопахорское, квартал № 171